Thanks to BIM! Preventing bottlenecks on the construction site
Switzerland
/
Messeplatz, Basel
2019-2021
|
Balintra AG, represented by UBS Fund Management (Switzerland) AG (SIMA)
Architect:
Morger Partner Architects AG
|
Budget:
CHF 96 million
The Clara Tower in Basel presented us with a logistical Herculean task. However, with the help of a “digital twin”, we were able to precisely predict and plan the construction process. This led to efficient, process-controlled production. We also achieved significant cost and schedule security.
emphases
Continuous BIM planning and use of the digital twin also for digital logistics
BIM2LOG
Process-controlled construction logistics
Space management
Personnel logistics during COVID
The project
The Clara Tower is a 31-storey high-rise building with an adjoining annex opposite the Basel exhibition center. Built according to designs by Morger Partner Architects, the almost 100 meter high tower primarily contains apartments. There are also commercial and catering spaces on the ground floor.
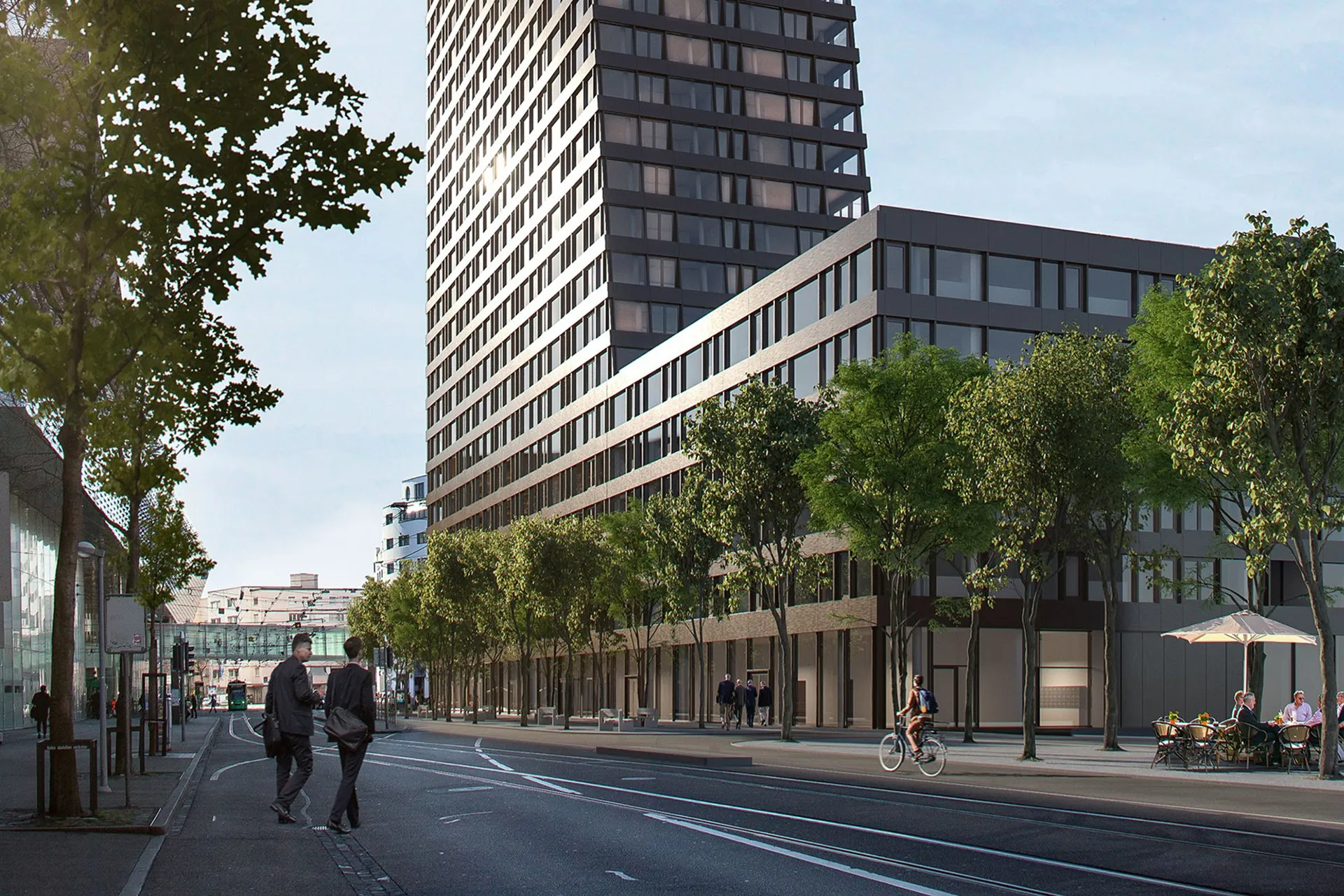
challenges
13 000 m²
of glass surfaces, 1275 inserts, 8 km of ventilation ducts, up to 32 truck trips with just one access per day: In order to get this volume to the right floor areas within one and a half years, operational construction logistics handled over 4000 deliveries and provided over 810 hours of outdoor lift service. At peak times, more than 300 employees worked on the construction site at the same time.
In short: The Claraturm construction project required a logistical masterpiece.
solution
Together with Halter general contractor We developed the “Digital Logistics” competence center to embed process-controlled production on Halter AG construction sites. An important preliminary work for the Claraturm project: Using a so-called digital twin, we were able to precisely logistically simulate the complex Basel construction project at the Competence Center. The digital twin belongs to the core of the so-called Building Information Modeling (BIM) method). With its help, as much building information as possible is digitally modelled in advance. This made it easy to prefabricate façades, sanitary installation elements and entire prefabricated wet cells of the Clara Tower. This resulted in ideal process-controlled logistics for us. We were able to use this information to link it to the schedule and generate an ideal delivery flow for the construction site (BIM2LOG). This schedule starts with the regulated number of truck trips, goes through the best timing of the elevators to better utilization of storage space on the construction site, controlled centrally via CLM.
.jpg)
“The Clara Tower's digital twin was almost error-free and therefore an important basis for decision-making.”
scores
The Claraturm project shows how we can improve efficiency and productivity in the construction industry with data-based software solutions. Thanks to BIM (BIM2LOG) and digital twin, all project participants worked together much better and more efficiently. In addition, access control for people on the construction site as well as deadline and cost security were ensured despite COVID.
Diego Frey from Halter AG assumes that digitization, integrated collaboration and increased productivity in the construction industry can reduce costs and deadlines of 30 to 40% within five to seven years. For Frey, there is no question that the construction industry must move. In recent years, it has hardly increased productivity at all, in contrast to other industries.