Migros: Branch remodeling made easy
Switzerland
/
Various branches, Zurich
2018-ongoing
|
GMZ Genossenschaft Migros Zürich
Architect:
Diverse planning teams
|
Budget:
Approx. CHF 12-15 million per branch
Migros regularly modernizes its branches in order to offer a contemporary shopping experience. In doing so, it wants to keep branch closures and restrictions as short as possible. That is why Amberg Loglay AG and Migros Zurich developed the “SMARTER building strategy” or the so-called TOPB: time-optimized planning and construction.
emphases
Process-controlled construction logistics
Space management
Prefabrication
Consolidation center and HUB logistics
Just-In-Time
The project
Migros Zurich is already rebuilding its sixth branch using the SMARTER build principle, which it developed together with Amberg Loglay. Migros is thus achieving optimised logistics planning, which reduces construction time by 50 percent.
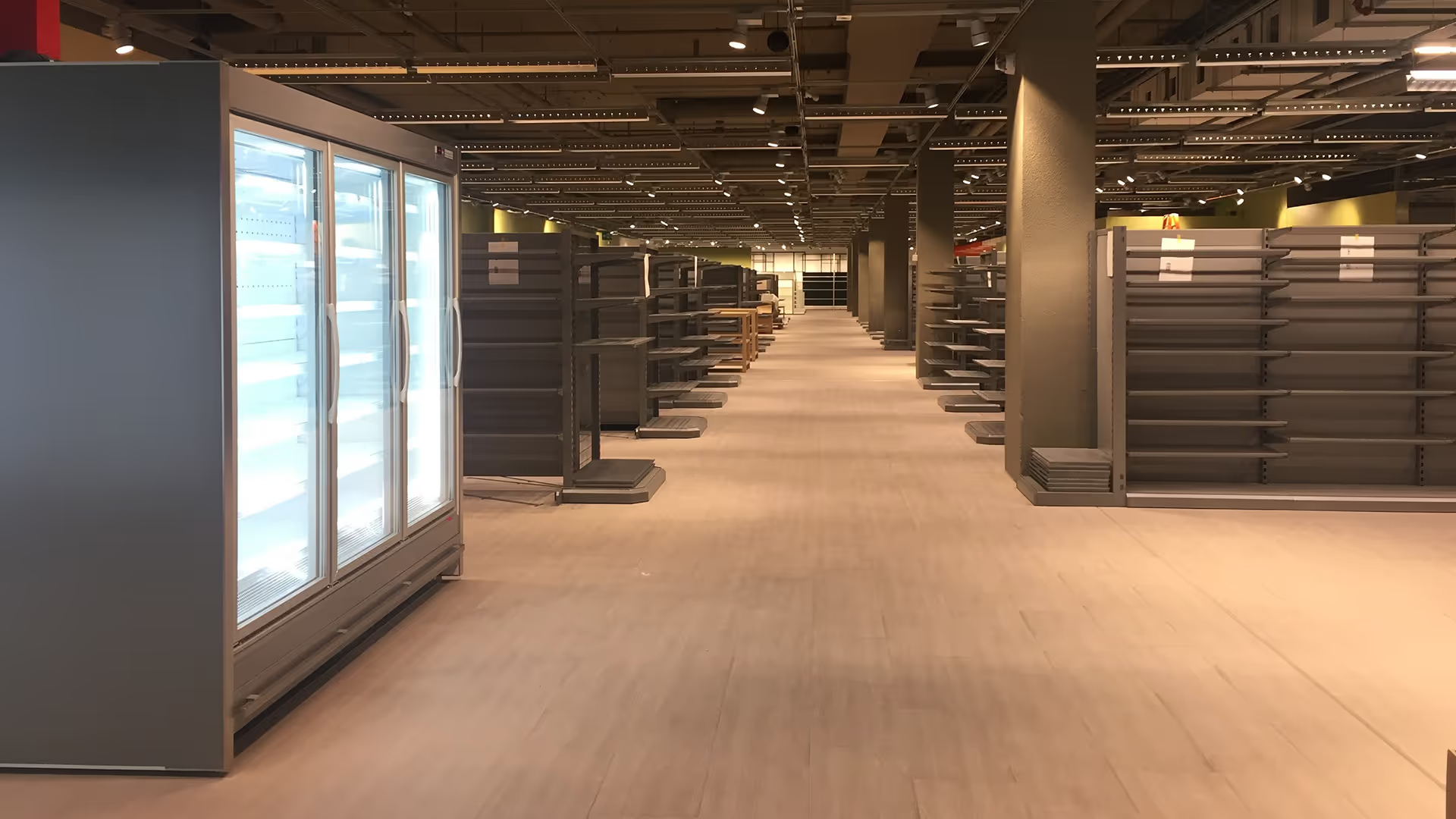
challenges
When renovating Migros branches, a variety of stakeholders are involved and isolated planning tools are used. This results in duplication and inefficient processes, which increases costs and extends construction time. To counteract this, the Migros Zurich cooperative turned to Amberg Loglay. Your questions were: How can we consolidate work activities and make optimal use of resources? How can we also meet the needs of long-standing employees at the same time?
solution
Model-based logistics planning was carried out before the rebuild. This includes a quantity-based analysis in order to provide an ideal material flow in time and space and to plan all resources accordingly. In the Brunaupark project, we determined whether the conversion (dismantling, new construction, furnishing and commissioning) could be carried out within the period specified by Migros Zurich and what resources are required for this. The experience gained from renovating the Migros branches in Volketswil and Dübendorf helped. In a rough analysis, we determined the material quantities and material turnover and projected the data over the specified period of time. At high altitude, for example, we predicted which resources and measures would be necessary to complete the conversion in the desired time. In interdisciplinary workshops, we then planned the construction process backwards — from the end, i.e. completion and handover. In doing so, we coordinated the work precisely with logistics. The analysis thus resulted in a schedule based on “time-based space planning,” which would be preceded by a consolidation center. Two branches have already been able to manage the flow of deliveries via such a consolidation center. The goods are stored there in large deliveries and then brought to the construction site on a daily basis. This reduces lack of space and traffic jams on the construction site, goods remain safe and clean and are installed efficiently. Central disposal logistics also ensures a high separation rate, which is standard in downtown Zurich — but can rarely be implemented due to lack of space.
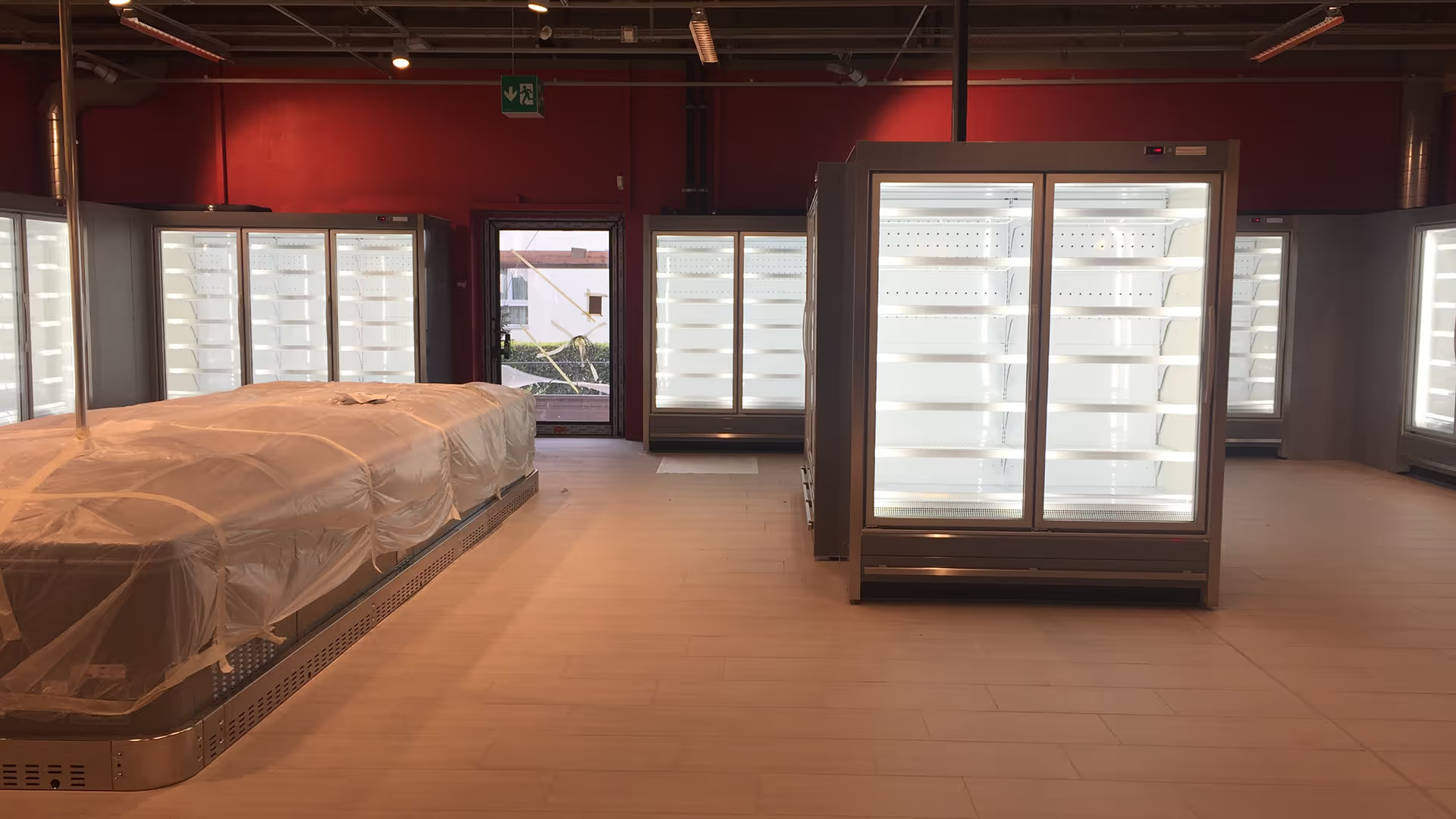
«Digitalization first requires an investment in the design of new processes and technologies and their integration into the project organization.»
scores
Based on these considerations, together with the Migros Zurich Cooperative (GMZ), we developed a SMARTER building strategy that enables time-optimized construction and planning (TOPB). On a project-specific basis, instruments determine how much logistics and time-optimized processes are required for the respective construction phase. This procedure is no longer only used for so-called maxi projects, which have integrated construction logistics including a consolidation center (HUB) and model analysis. It also makes it possible to support the construction of smaller branches. The TOPB strategy has proven successful: Thanks to the branch projects implemented so far, Migros Zurich learned how to optimize the various processes and create a good working atmosphere for everyone involved in the construction project. Migros employees know the processes, the project teams use standardized documents and the number of projects is constantly being refined, which makes planning more efficient and successes comparable. In this way, Migros is also helping to reduce traffic jams and emissions in front of its construction sites in the Zurich urban area, supports sustainability through good waste separation and less waste, and is committed to digitizing construction processes. The planning of a sixth branch based on this principle is currently underway.