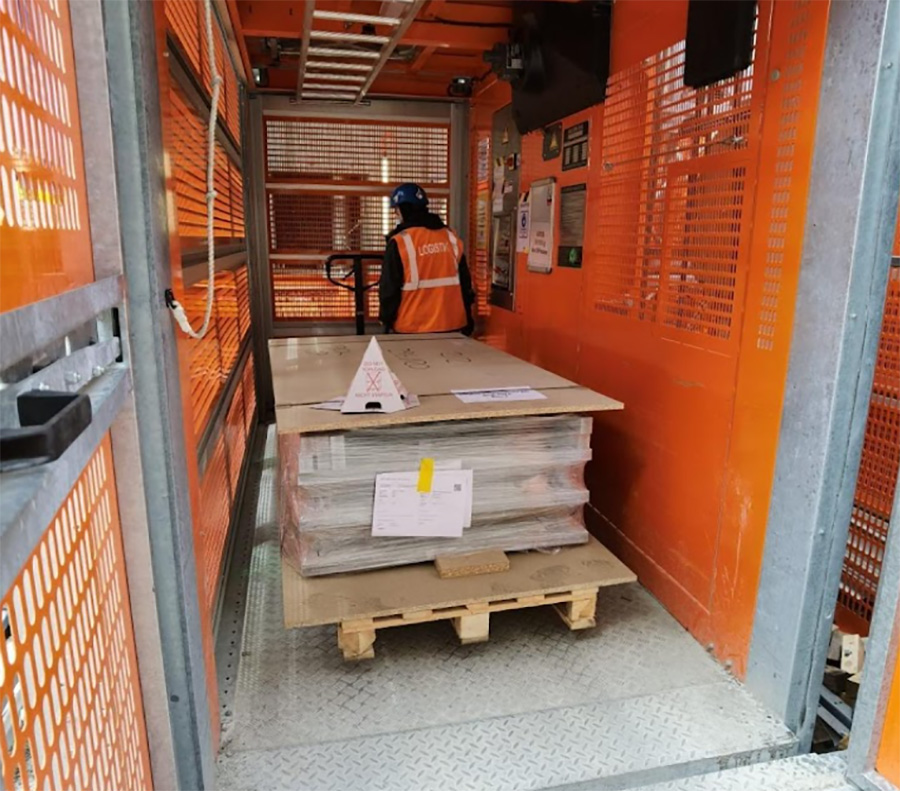
Hustle and bustle on construction sites
There is a hustle and bustle on a large construction site. Different people do different work side by side. If these are not optimally coordinated, there are waiting times. Arriving and waiting at the elevators in particular is one of the time thieves par excellence. With just 15 minutes of waiting per day per person, this results in 50 hours of waiting (for 200 people) and that per day — an unbelievable potential for added value!
Specifically, the aim is to minimize costs for the client while minimizing waiting times and optimal transportation of materials.
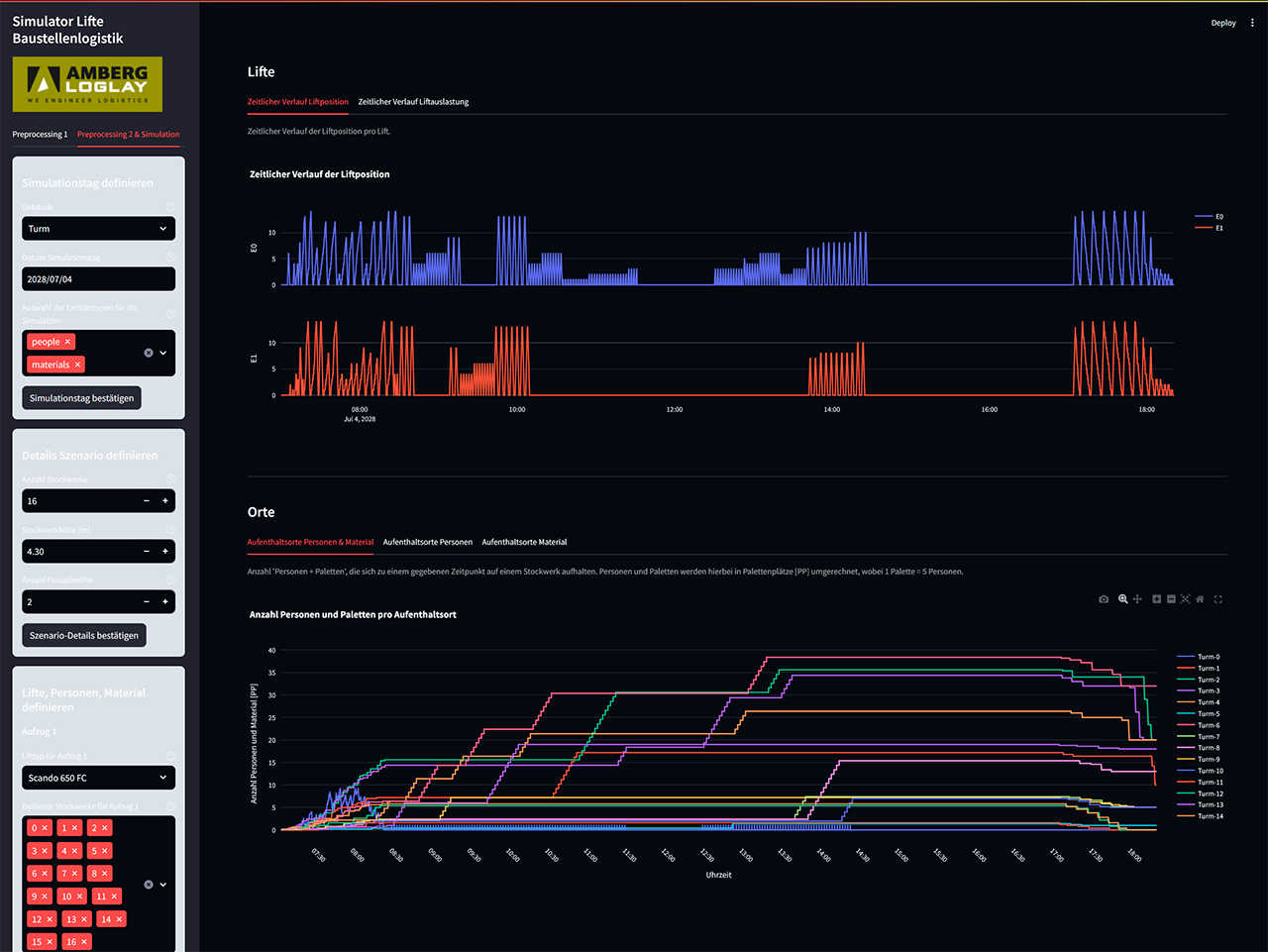
Simulation for optimal flow efficiency
The simulator is intended to support planning teams in all aspects of logistics, from strategic planning to daily operations, and ultimately to value creation.
In addition to optimizing logistics planning, the simulator enables the project team — regardless of their simulation expertise — to quickly evaluate various planning scenarios in order to size the optimal equipment for their construction project. This user-friendly approach is intended to significantly improve decision quality and acceptance thanks to intuitive visualizations and a focus on real applications. For example finding optimal transportation strategies for materials and personnel to reduce waiting times. The project also values sustainability and aims to minimize environmental impact and improve the urban environment through better logistics coordination.
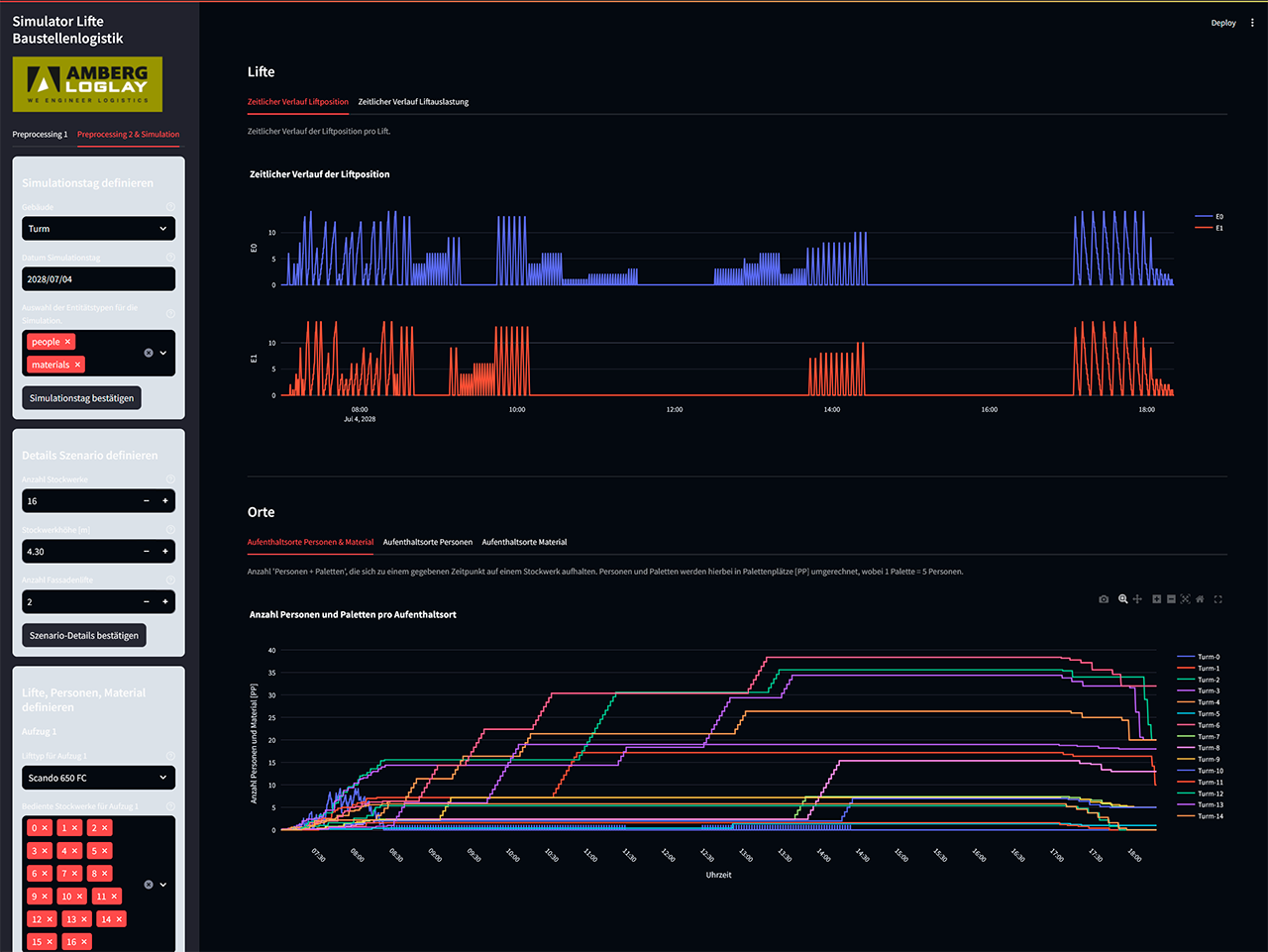
Modeling scenarios — what is it about?
When specific deliveries have been announced (time, quantity, target floor have been determined) and disposal volumes have been defined, it should be determined how to optimally carry out the material flows on the construction site:
- Which delivery should be assigned to which unloading point and which lift? Make optimal use of lifts and unloading to alleviate capacity bottlenecks in advance
- Can the entire delivery go directly to the storage area on the target floor or does material have to be temporarily stored somewhere else?
- According to which rules are lift trips coordinated? (e.g. always drive as full as possible, i.e. take disposal material as far as possible on the way down)
Project teams use simulation to:
- Analysis of material and personnel volumes over the project period.
- Analysis of different scenarios:
- Number and type of construction lift, operating times, timetables/driving strategies, load scenarios, effects on failures, faults, modifications
- Comparison of different scenarios, detailed reports, best-case/worst-case analysis

Creating value through cooperation
The initiative was launched by Amberg Loglay as a pioneer for data and simulations in construction logistics. In a strategic collaboration with key players in the sector, including Post Baulogistik AG, Halter AG, Alimak Group Swiss AG, together with IMS Institute for Modelling and Simulation at the University of Applied Sciences in Eastern Switzerland, each of which contributes their expertise in the areas of logistics, construction services, vertical transport and simulation methods.
Together, we have developed a user-friendly simulation tool that increases efficiency on the construction site and promotes collaboration between stakeholders.
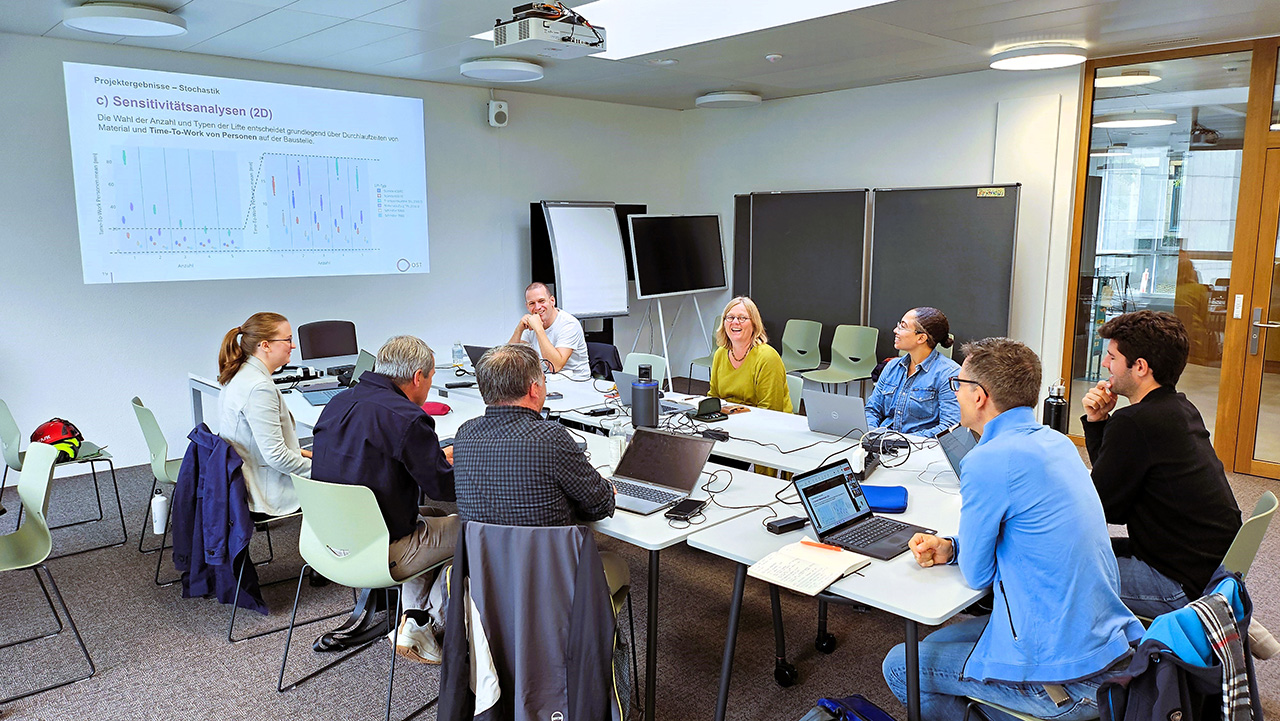
Innovations for the sector
Amberg Loglay has been changing the market for several years now with the introduction of its simulation-based applications. This innovative initiative expands the portfolio. It aims to eliminate the significant delays that stress construction projects and can account for up to 40% of working time.
By using the power of simulation, optimization, and machine learning, we strive to improve the efficiency of material, equipment, and personnel flows on construction sites, reducing disruptions and improving overall project results.